

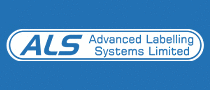
Labelling Machines
Labelling Machines apply labels and decoration onto all types of packaging containers, display, point-of-sale and transit packs.
There are two principal types of labelling machines: Wet Glue and Pressure Sensitive (Self-Adhesive) applicators. These and their variants, plus special purpose machines, are listed in the detail sections below.
Branding and promotional labels
Labels are used on every kind of product to brand and decorate packaging to communicate brand identity and motivate consumer purchase. There are multiple options for brand owners to choose from, including different substrates, embellishments and customisation, as well as a range of quality levels and finishes.
Information labels and barcode labels
Many labels contain pre-printed barcodes supplying batch, stock and price information to the retailer and consumer. Other machines provide print-on-demand and weigh/price labels, usually for fresh or perishable products where the weight of item varies from pack to pack or for transit purposes. Many of these labels are printed and applied in the store or warehouse.
Tamper-proof labels
Labels are also used to provide protection against tampering to ensure the product reaches the consumer unopened and without interference. Sleevers or sleeving equipment, which apply a sleeve of thermoformable or stretch material to the neck or body of the container, are generally used to apply tamper-evident labels. Shrink-sleeve labels are also used on products which do not have surfaces suitable for a conventional label.
Security labels
A growing market is security labelling to counter fraud and theft, and give brand protection and authentication. These include RFID and smart labels, holographic labels, tamper evidence, counterfeit deterrence and source tagging. Other machines are used to apply leaflet labels – multi-page labels that provide space for large amounts of consumer information, e.g. in pharmaceutical applications.
Further types of labelling
Other types of labelling include in-mould labelling, a technique that applies labels to blown bottles, injection moulded containers, and thermoform fill seal machines for yoghurt pots, as they are formed on equipment.
What are the main trends in labelling?
Lightweight labels
The drive to reduce weight in packaging includes a move to smaller, lighter and thinner materials for labels. The benefits include significant reduction on paper and substrate usage.
Recyclable labels
While labels are a relatively small component in packaging, they affect recyclability through the use of materials and adhesives. The growing focus on recycling has resulted in the development of new adhesives which do not inhibit recycling processes.
Automation in label printing
Streamlined workflows in integrated packaging and labelling lines are increasingly being driven by sophisticated systems which ensure maximum efficiency for short and longer run operations.
Digital label printing
Digital printing and data systems enable increased options for customisation and speed of production. There are also advances in digital print quality using toner and inkjet technology, and in compatibility with automated systems.
Premium labels
The look and finish of a label has a high level of influence on consumer demand. Expensive-looking labels with high quality images, varnishes and other embellishments increase shelf-appeal.
What are the types of labelling machines?
Wet Glue Labelling Machines
Wet glue labelling machines apply labels using a glue which is liquid at room temperature. These machines usually apply labels from a stack to rigid containers, such as beer or spirit bottles at very high speeds.
The machines are particularly suitable for wet environments, such as liquid filling of beverages where they continue to be the predominant application method. Often the labels are highly decorative and can be embossed and cut into complex shapes, or are applied to difficult container shapes. Often more than one label is applied to one container, requiring several applicators.
Since the 1960s, Pressure Sensitive labels have become more popular for most other types of applications. They are used extensively in the beverage sector.
Hot Melt Label Applicators
Machines which apply labels using adhesive which is solid at room temperature.
Hot melt label applicators are a variant of the Wet Glue Labeller, where different types of adhesive are heated to a liquid state prior to application. The adhesive may vary due to the product, packaging material or external conditions in the packaging area. This type of applicator is, for example, used for wraparound labels that cover most of a container body and wall surface.
Pre-Gummed Label Applicators
Pressure-Sensitive Self-Adhesive Label Applicators
Pressure-sensitive labelling machines use pre-glued labels supplied on a reel of release paper or film. They require no water to make the adhesive stick.
Due to their popularity, they have replaced many traditional forms of wet glue application. The advantages are that there is no liquid glue or heat required in the process and the label can be made from materials other than paper. The labels can be pre-cut into complex shapes on the reel by means of a die-cutter and stored on the reel until required, with minimal risk of damage. This method of application enables labels to be applied at medium/high speed to soft packages, as well as rigid containers and where the product could be damaged by water or heat.
Heat-Seal Label Applicators
Print & Apply Label Applicators
Print and Apply labelling machines can be loaded with information which is used to print labels on demand with details including batch number, production date, weight, price and transit data, as well as simple graphics.
Common forms of Print & Apply Labeller are those used by retailers to print weight and price information at the point of sale. Products such as meat, fresh fruit and vegetables and other types of product which are not pre-packed prior to arriving in the supermarket use this method of labelling. Often the labels include a barcode for scanning at the checkout.
Print & Apply labelling equipment is also used in warehousing and distribution to provide delivery, batch and other transit information. This allows the product to be traced, and can confirm that the product has arrived where it should, on the correct date and in the right quantity. The label can be printed directly on to the outer transit container or on to a label which is then applied to the transit container. Information can be printed in both standard type and as a barcode.
Decorating Equipment for Packaging Machines
Tag Labeller
Capsuling
Foiling (Neck Foiling)
Sleeving Machines
Shrink Sleeving Machines
Stretch Sleeving Machines
Common Terminology
- Application heads
- Release paper
- Feeder
- Stack
- Roll
- Sheet
- Glue reservoir
- Hot melt applicator
- Register mark
- Glue applicator
- Printers
- Applicators
- Blow labeller
- Thermal transfer
- Pad printer
- Print Resolution
LABELLING MACHINERY
Search for PPMA members companies who can provide Labelling Machines to assist with your next labelling project.